Â
In the meticulous production world, the roles of Quality Assurance (QA) Technicians and Quality Control (QC) Inspectors are paramount. These professionals act as guardians of quality, ensuring that products and services meet established standards and regulations. From the food we eat to the cars we drive to the electronics we rely on daily; these behind-the-scenes experts significantly contribute to the quality of our everyday lives.
However, their commitment to excellence comes with risks. The environments in which QA Technicians and QC Inspectors work are often fraught with potential hazards. Exposure to harmful substances, the operation of heavy machinery, and the intricate handling of various products are just a few aspects of these roles that pose significant risks. Thus, the need for comprehensive safety protocols and personal protective equipment (PPE) is not a mere regulatory compliance stipulation but a critical necessity.
This article explores the intricate roles of QA Technicians and QC Inspectors, highlighting the safety considerations intrinsic to their professions. We delve into the dynamics of their daily responsibilities, examine the potential hazards they encounter, and underscore the protective measures vital to ensuring their safety and, by extension, the quality assurance of countless products that shape our modern world.
Â
Â
Quality Control Inspectors
Â
Â
Quality control inspectors are vigilant overseers in manufacturing and production industries. They conduct thorough inspections of products, materials, and processes, ensuring that all meet predefined standards and regulations. Identifying defects and inconsistencies prevents substandard products from reaching consumers, thereby maintaining the brand’s integrity, and ensuring end-users' safety.
The tasks of a QC inspector often include:
- Detailed examination of products through various stages of production.
- Use of specialized testing equipment to assess quality parameters.
Â
Â
(QA) Quality Assurance Technicians
Â
Quality assurance technicians operate within a broader spectrum, focusing on the systemic aspects of quality management. They ensure production processes are designed and executed to meet internal and external quality standards. Their approach is more preventive, concentrating on avoiding product defects rather than identifying them post-production.
The tasks of a QA technician often include:
- Monitoring and auditing of production processes.
- Conducting risk assessments and implementing preventative measures to avoid lapses in product quality.
Â
Additional Quality Control Roles
Â
According to O*NET OnLine, both Quality Assurance and Inspection encompass numerous job types and roles. Here, we highlight these roles, explaining their responsibilities, contributions to maintaining quality standards, and varying safety concerns:
Â
- Inspector: Examines products, materials, or processes to ensure they meet specified requirements, focusing on identifying defects or deviations from standards.
Safety concerns: Physical hazards depending on the industry (e.g., manufacturing, construction), risk of exposure to hazardous materials, and potential repetitive strain injuries.
Â
- Quality Inspector: An inspector inspects products, processes, or materials to ensure they meet quality requirements, working in industries such as manufacturing and construction.
Safety concerns: Include physical hazards, including machinery, hazardous substances, and environmental risks, risk of injury from manual handling or lifting heavy objects, and possible exposure to extreme temperatures or noise levels.
- Quality Control Inspector (QC Inspector): This position ensures products meet quality standards before release or shipment, using various tools and techniques to detect defects.
Safety concerns: Include exposure to production environments with machinery and moving parts, risk of slips, trips, and falls in industrial settings, and handling hazardous materials or substances during inspections.
Â
- QC Technician (Quality Control Technician): This position tests and inspects products or materials to ensure they meet quality standards and specifications.
Safety concerns: High risk of physical injury from working on production lines, exposure to noise, dust, and chemical fumes, and risk of repetitive strain injuries.
- Quality Auditor: This position conducts audits of quality management systems, processes, and documentation to verify compliance with standards and regulations.
Safety concerns: Generally minimal physical risks, ergonomic issues from extensive computer work, and travel-related risks if audits are conducted off-site.
- Quality Technician: Supports quality assurance and control activities by performing tests, inspections, and data analysis, as well as assisting in troubleshooting quality issues.
Safety concerns: Working with various testing equipment that could present electrical or mechanical hazards, exposure to hazardous chemicals or materials, and ergonomic concerns from repetitive tasks.
- Test Technician: Conducts tests and evaluations on products, components, or systems to verify performance and identify defects or issues.
Safety concerns: Risks from handling and operating testing equipment and machinery, exposure to electrical hazards if working with electronic components, and chemical.
Â
Â
Employment Landscape
Â
Recent statistics show that the quality control sector employs approximately 595,400 individuals, significantly contributing to the global workforce.
These professionals span various industries, indicating the universal necessity for quality assurance in production. The manufacturing sector holds the majority share, employing 64% of all quality inspectors. Other sectors, including professional, scientific, technical services, administrative and support services, and wholesale trade, also comprise key employment areas.
The table below represents the distribution of employment for all the quality and inspector roles mentioned above in the manufacturing industry across various states and industries. This matrix provides insights into which sectors, and geographical areas employ the most professionals in this occupation.
Inspectors and Quality Assurance Employment in Manufacturing
State |
MFG Employment |
Total |
California |
36,180 |
57,120 |
Ohio |
21,960 |
28,290 |
Illinois |
21,080 |
31,100 |
Texas |
20,760 |
52,220 |
Michigan |
18,660 |
29,630 |
 North Carolina |
17,330 |
19,900 |
 Indiana |
15,840 |
19,930 |
 Pennsylvania |
15,430 |
19,260 |
Wisconsin |
13,850 |
17,630 |
New York |
13,840 |
20,950 |
Â
Â
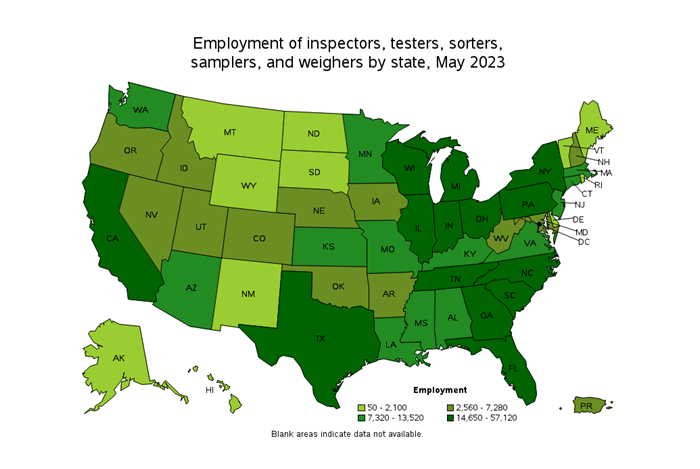
From this chart we can observe:
- Manufacturing Sector Dominance: Across the board, manufacturing remains the dominant employer for quality control roles, with 379,520 quality inspectors employed. This trend is consistent across all states, underscoring the critical need for quality control in manufacturing industries. States like California, Ohio, Illinois, Texas, and Michigan have a high concentration of manufacturing activities. These states are traditional industrial centers, with industries ranging from automobile manufacturing in Michigan and Ohio to technology and aerospace in California and Texas. The presence of these industries requires stringent quality control, thereby employing a significant number of quality control inspectors.
- Diverse Industry Opportunities: While manufacturing takes the lead, there's notable employment in professional, scientific, and technical services, indicating the role's relevance across diverse industries. California has many roles within the Computer and Electronic Product Manufacturing sector. This concentration is likely due to the state's status as a tech hub, particularly in regions like Silicon Valley, which demands high precision and quality in product manufacturing. States like Illinois, North Carolina, and Indiana have diverse manufacturing industries, from machinery, chemicals, and plastics to pharmaceuticals. The necessity for quality assurance across such a wide range of products contributes to the demand for professionals in inspection and testing. Below is a breakdown of the top industries employing Inspectors and Quality control personnel.
Industry |
 Employment |
 Plastics Product Manufacturing |
31,320 |
Architectural and Engineering Services |
28,410 |
Motor Vehicle Parts Manufacturing |
23,710 |
Aerospace Manufacturing |
20,710Â |
 Foundries |
6,090 |
Â
Â
Â
Â
Work Activities and Associated Risks
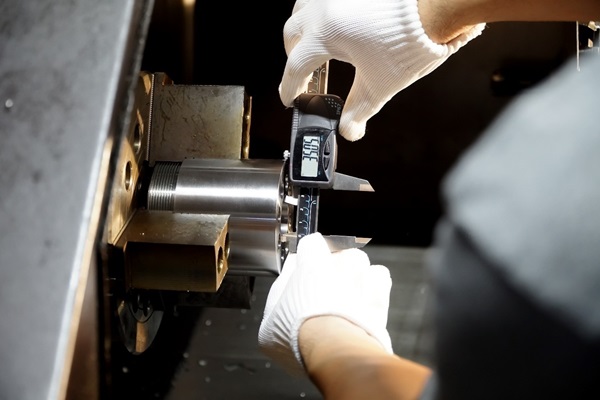
Â
Quality control inspectors ensure product safety, functionality, and quality, but they often face workplace hazards, leading to various injuries. As our first table below shows, over 9,000 injuries affected these workers in 2022. Their hands are among the most injured body parts, second only to injuries affecting body systems. These body system injuries include conditions impacting the respiratory, cardiovascular, and nervous systems, often resulting from exposure to hazardous substances or high-stress environments.
Occupational Code 51-9060
Rank |
Total Cases |
9,360 |
1Â |
Body systems |
2,560 |
2 |
Hand |
880 |
3 |
Trunk - Back |
810 |
 4 |
Multiple body parts |
800 |
5 |
Knee |
520 |
6 |
Shoulder |
450 |
7 |
Arm |
350 |
8 |
Foot |
310 |
9 |
Wrist |
290 |
10 |
Ankle |
270 |
11 |
Head - Eye |
190 |
 12 |
Neck |
90 |
Â
Â
The matrix below outlines typical activities completed by these workers, the potential hazards, and the injuries that might occur if these risks are not properly mitigated.
Task/Activity |
Hazard Concern |
Potential Injury |
 Cleaning and repairing
equipment or instruments |
Exposure to toxic substances; risk
of physical injury from tools or equipment |
 Chemical burns, cuts, or respiratory issues |
Collecting samples for testing |
Exposure to hazardous materials; biological risks |
Skin contamination, inhalation of toxins |
Electrical and fabrication tasks |
Electrical hazards; flying particles, sharp objects |
Electrical shock, eye injuries, cuts |
Equipment operation |
Improper use of equipment or machinery failure |
Crush injuries, fractures, sprains |
Handling and positioning workpieces |
Heavy lifting; sharp or hot materials |
Musculoskeletal injuries, burns, cuts |
Handling of materials |
Risk of cuts, lacerations, and punctures
from sharp objects or machinery |
Cuts, lacerations, puncture wounds |
Inspection and testing |
Exposure to harmful substances or environments (e.g., toxic chemicals, loud noises)Â |
Chemical burns, respiratory issues, hearing loss |
 Inspecting sustainable energy facilities or equipment |
High-altitude falls; electrical hazards |
 Falls, electric shock |
Marking products or measuring dimensions |
Repetitive motion; sharp objects |
 Strains, cuts |
 Smoothing metal surfaces |
 Flying particles; noise, chemical exposure |
Eye injuries, hearing loss, skin irritation |
Sorting and stacking materials or products |
Repetitive motion; heavy lifting |
Strains, musculoskeletal injuries |
Testing chemical or physical characteristics |
 Exposure to hazardous chemicals, toxic substances |
Chemical burns, respiratory issues, eye injuries |
 Weighing materials or products |
 Heavy lifting; hazardous materials |
 Musculoskeletal injuries, skin contamination |
Â
The matrix above outlines the various daily tasks and associated hazards that quality control inspectors and QA technicians face. Understanding these specific risks is crucial for developing effective safety measures. Now, let’s delve into the common safety hazards encompassing these activities and explore the broader implications for worker health and safety.
Â
Common Safety Hazards
Â
Â
Quality control inspectors face a myriad of hazards in their daily operations. If not adequately managed, these hazards can lead to severe injuries or health issues. Below, we highlight some of the main hazards and their implications:
- Exposure to Harmful Substances or Environments: This is a prevalent hazard, especially for inspectors dealing with chemical products or working in industrial environments. Harmful substances can lead to chemical burns, respiratory issues, and long-term health complications. For instance, BLS data shows exposure to harmful substances as the number one cause of injury incurred by workers.
Occupational Code 51-9060
 Rank |
Total Cases |
9,360 |
 1 |
Exposure to harmful
substances or environments |
2,640Â |
 2 |
Falls, slips, trips - Total |
2,290 |
3Â |
Contact with object, equipment - Total
|
 1,980 |
 4 |
Overexertion and bodily reaction - Total |
 1,870 |
 5 |
Overexertion in lifting or lowering |
 480 |
6Â |
Transportation incidents - Total |
 480 |
7Â |
 Repetitive motions involving microtasks |
340Â |
 8 |
Roadway incidents involving motorized land vehicles |
 170 |
Â
- Physical Hazards from Tools or Equipment: Inspectors often interact with various tools and machinery, which, if malfunctioning or misused, can cause injuries like cuts, lacerations, or more severe trauma such as fractures or crush injuries. Data from the Bureau of Labor Statistics suggests a high incidence of such injuries, underscoring the need for rigorous safety protocols and proper personal protective equipment (PPE).
Â
Â
 |
 Occupational Code 51-9060 |
 |
Rank |
Total Cases |
9.360 |
1Â |
Sprains, strains, tears |
2,030 |
2 |
Soreness, pain |
1,150 |
3Â |
Bruises, contusions |
810 |
4 |
Fractures |
780 |
 5 |
Cuts lacerations |
520 |
6 |
Punctures (except gunshot wounds) |
100 |
7 |
Amputations |
50 |
8 |
Chemical burns and corrosion |
40 |
9 |
Carpal tunnel syndrome |
40 |
10 |
Heat (thermal) burns |
30 |
Â
Â
- Electrical Hazards: Those inspecting electronic equipment or sustainable energy facilities are at risk from electrical hazards. Improper handling of electrical components can lead to shocks, burns, or, in severe cases, fatalities.
- Hazardous Material Handling: Handling sharp objects or dangerous materials without appropriate protective gear can easily result in cuts, punctures, or skin contamination. This risk is exceptionally high in environments with metal, glass, or chemical substances.
Â
Each hazard requires specific safety measures, including appropriate PPE, adherence to safety protocols, regular health checkups, and ongoing safety training. By understanding and mitigating these risks, workplaces can significantly reduce the incidence of injuries associated with quality control inspection tasks.
Â
Â
Â
Eye Injury Sources
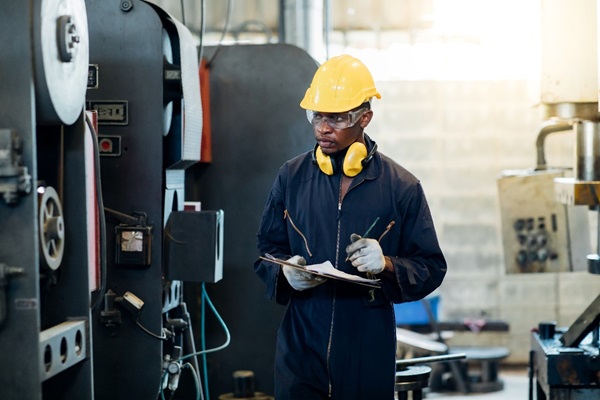
Â
Eye injuries in the workplace, particularly among quality control inspectors, can occur during various tasks where there is a risk of exposure to harmful substances, flying particles, large machinery, or intense light sources. Here are some of the activities where eye injuries are more prevalent:
- Cleaning and repairing equipment or instruments: This task involves exposure to chemical agents, dust, or small detached particles during the cleaning or repairing process, all of which pose a risk to the eyes.
- Electrical and fabrication tasks: These activities can expose workers to sparks, metal shavings, or other particulates that can cause eye injuries. Additionally, working with electrical systems may involve bright flashes or arcs that can harm the eyes.
- Inspecting sustainable energy facilities or equipment: The inspection may involve exposure to intense light, dust, or other environmental factors that could cause eye strain or harm the eyes.
- Handling and positioning workpieces: Handling materials or components can involve risks from flying particles, especially if the materials are being cut, drilled, or manipulated in ways that produce debris.
- Smoothing metal surfaces or grinding: These tasks can generate flying particles, shards, or dust, posing a significant risk of eye injuries.
- Inspection and testing: This involves closely examining products or materials, potentially exposing inspectors to harmful substances, sharp object projections, or other hazards that could harm the eyes.
- Equipment operation: Operating heavy or complex machinery can expose workers to various hazards, including flying particles, chemical splashes, or intense light, all of which are hazardous to eye health.
- Testing chemical or physical characteristics: Handling chemicals or hazardous substances can risk splashes or vapors entering the eyes, leading to irritation, burns, or other eye injuries.
- Marking products or measuring dimensions: These tasks, especially if cutting or marking materials, can produce particulates or shavings that may get into the eyes.
Appropriate eye protection, such as safety glasses, goggles, or face shields, is crucial in each activity. These protective measures and adherence to safety protocols help mitigate the risk of eye injuries.
Â
Â
Hand Injury Sources
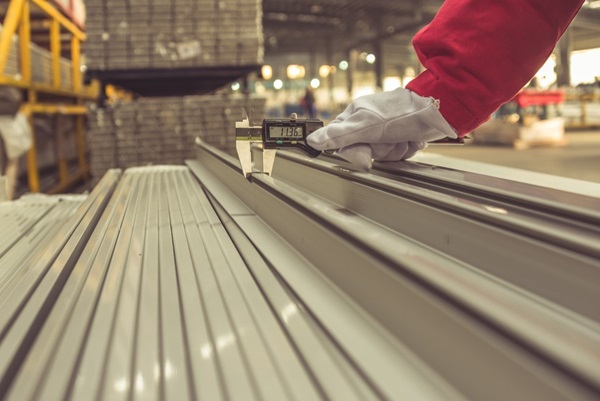
Hand injuries are common in environments where workers handle machinery, tools, or hazardous materials. Specific tasks pose a higher risk of hand injuries for quality control inspectors and similar professionals. Here are some of the activities where such risks are prevalent:
- Cleaning and repairing equipment or instruments: Handling tools, equipment parts, or chemicals without proper protection can lead to cuts, abrasions, burns, or other hand injuries.
- Collecting samples for testing: This might involve handling sharp objects, corrosive chemicals, or hazardous materials, which can lead to potential cuts, punctures, chemical burns, or irritations.
- Electrical and fabrication tasks: Exposure to electrical components or using tools in fabrication can result in burns, electrical shocks, cuts, or lacerations.
- Handling and positioning workpieces: Manipulating raw materials, components, or heavy items can expose workers to risks such as cuts, crush injuries, or pinching from handling heavy or irregular objects.
- Smoothing metal surfaces or grinding: These tasks involve using tools or machines that can produce sparks, flying debris, or sharp edges, all of which pose a risk of cuts, abrasions, or burns.
- Sorting and stacking materials or products: Handling, moving, and organizing products or materials can lead to repetitive strain injuries, cuts, or crush injuries if materials are cumbersome.
- Weighing materials or products: Cuts, lacerations, or punctures from sharp edges or pinch points might occur, depending on the materials involved.
- Testing chemical or physical characteristics: Handling chemicals or hazardous substances can risk chemical burns, allergic reactions, or other skin irritation.
<OTHERS
oled display microlens optica,oled display microlens quantum,anti reflective coating in solar cell,anti reflective coating polarized lenses
Ningbo Merak Advanced Materials Technology Co., Ltd. , https://www.merak-tech.com